According to the Senseye report by Siemens AG, predictive maintenance (PdM) powered by Artificial Intelligence reduces your costs by up to 40% and cuts unplanned downtime by a massive 50%.
How does it work?
Predictive maintenance uses advanced technology, such as AI and the IoT, to predict when machines need upkeep.
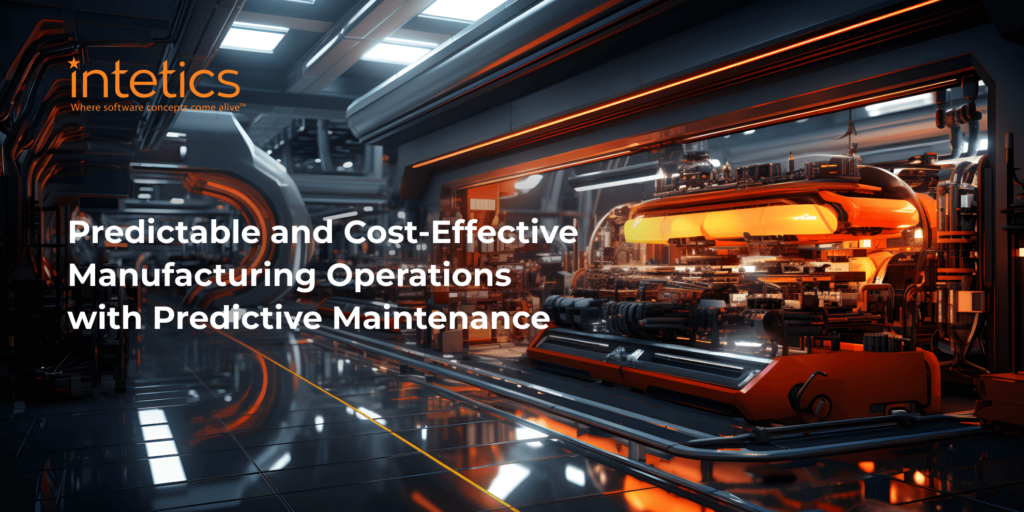
For example, if the equipment starts to overheat, the system doesn’t just sit there. It alerts the right people—your maintenance crew or business managers. The goal is to spot problems before they become disasters.
Read more: What Is Predictive Maintenance?
Reactive vs. Preventive vs. Predictive Maintenance
How does predictive maintenance stack up against the standard reactive and preventive maintenance? Explore the three critical aspects of each approach:
Reactive maintenance:
- Wait and react—issues are fixed only after they occur.
- Higher costs—unexpected expenses may occur, such as production downtime and rush orders for replacement parts.
- Downtime troubles—operations can be disrupted at inconvenient times.
Preventive maintenance:
- Scheduled check-ups—maintenance is conducted on a pre-approved plan without considering whether the equipment needs it at that moment.
- Time-based—maintenance happens on a set calendar schedule.
- Goal—to prevent breakdowns with routine maintenance.
Predictive maintenance:
- Early detection—uses advanced tech to spot issues before they become critical problems.
- Timely alerts—sends warnings to the responsible employee when something’s amiss.
- Goal—to ensure that a piece of equipment needing maintenance is only shut down just before it’s about to fail.
PdM, a Solution to Critical Manufacturing Challenges
PdM tackles some of the most critical challenges faced by manufacturing professionals today:
- High maintenance costs: traditional maintenance approaches, like reactive and preventive maintenance, tend to over-maintain equipment or fix problems after they’ve been escalated.
- Inefficient inventory management: inaccurate maintenance planning results in a stockpile of spare parts that may not be needed.
- Unpredictable breakdowns and downtime: these are a nightmare for manufacturers, as they disrupt production, delay orders, and result in financial losses.
- Reduced equipment lifecycle: when machines aren’t adequately maintained, their lifespan shortens, necessitating costly replacements sooner than expected.
- Limited & outdated analytics: manufacturers need to rely on more accurate data for decision-making to avoid making suboptimal choices regarding maintenance and operations.
Taking these challenges into account, PdM delivers practical benefits that directly enhance a business’s financial performance and operational efficiency:
- Cost savings: addressing issues before they become significant problems saves on emergency repair costs and prevents production losses.
- Reduced downtime: predictive maintenance lets you know about potential problems so that you can plan repairs during scheduled downtime.
- Extended equipment life: regular monitoring and timely maintenance lengthen the life of your machinery.
- Optimized spare parts inventory: by predicting when and what parts you’ll need, predictive analysis simplifies inventory management and frees up funds for other investments or operational needs.
- Enhanced safety: well-kept equipment lowers the risk of accidents and makes your workplace secure for employees and the business.
- Boosted revenue: less downtime and improved production efficiency mean you can consistently meet customer demands, resulting in a higher revenue stream. It can also make a business more profitable by increasing supply capacity.
Featured Material: Supply Chain Automation: The Future of Streamlined Operations
PdM at a Glance
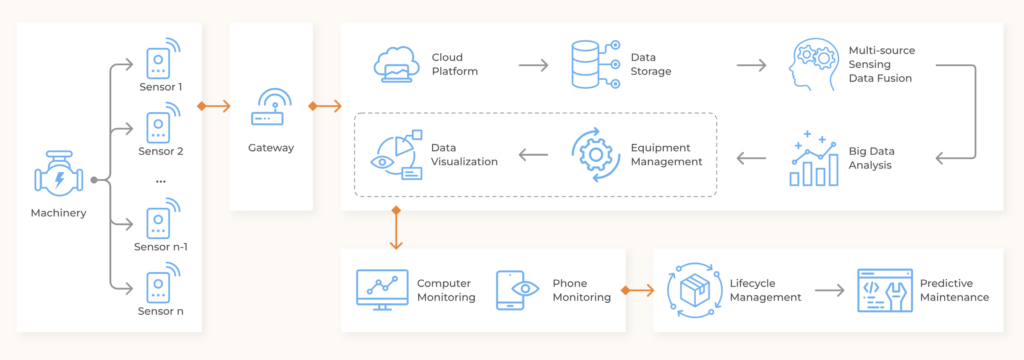
Facts and Figures: Predictive Maintenance Adoption Case Study
Indicative industry data shows the following outcomes of implementing predictive maintenance:
- Up to a 40% reduction in costs;
- Up to a 50% reduction in downtime;
- Up to a 55% increase in maintenance staff productivity;
- Up to an 85% improvement in downtime forecasting accuracy.
Discover a case study where we helped a business in FMCG to adopt a PdM solution.
A Swiss chocolate factory wanted to save resources and staff time, simplify operational processes, and improve data accuracy. For this, they started to modernize operations by integrating a PdM solution.
Inventory tracking was supposed to be optimized with the power of predictive analysis via a mobile application.
The developed mobile app swiftly identified and rectified inventory-related challenges, such as:
- excess or obsolete stock,
- tracking and recording the movement of goods,
- data accuracy, etc.
The result?
The business has increased productivity by 50% and saved significant costs and production time.
Which Industries Can Benefit from PdM?
Predictive maintenance solutions open advantages across a spectrum of industries:
- Oil & Gas
- Energy Production & Utilities
- FMCG
- Logistics and Transportation
- Machinery
- Automotive
- Construction
- Chemical
Things to Consider Before Adopting PdM for Manufacturing
The adoption of a complex PdM system requires substantial tech & industry experience. Expert support and managed innovation make the whole process predictable and cost-effective. And that’s how:
- Business-centric alignment: a comprehensive understanding of the business case and desired outcomes, ensuring that PdM systems are tailored to meet specific objectives.
- IoT infrastructure audit: assisted auditing of your IoT infrastructure and data assets to facilitate informed decision-making.
- Data foundation: establishing data integrity, consistency, interoperability, and security to provide a robust basis for PdM systems.
- Seamless transition: guided organizational transitions toward smarter and more efficient maintenance processes.
- User-friendly insights: providing user-friendly interfaces for real-time analytics and alerts to enable timely decision-making.
- Cutting-edge AI/ML models: designing and deploying multiparametric AI/ML models to leverage the latest technology for advanced predictive maintenance.
Predictive maintenance is currently the most advanced method for keeping industrial machinery in a desired condition. The need to upgrade your assets will only continue to grow. The right time to optimize your facilities is now.
Looking for a trusted partner in predictive maintenance solutions? Reach out today for expert guidance tailored to your specific manufacturing needs.